Specialist Guidance on What is Porosity in Welding and Just How to Address It
Specialist Guidance on What is Porosity in Welding and Just How to Address It
Blog Article
The Science Behind Porosity: A Comprehensive Guide for Welders and Fabricators
Understanding the complex devices behind porosity in welding is important for welders and fabricators aiming for flawless workmanship. From the make-up of the base products to the ins and outs of the welding procedure itself, a wide range of variables conspire to either intensify or alleviate the visibility of porosity.
Understanding Porosity in Welding
FIRST SENTENCE:
Evaluation of porosity in welding discloses essential understandings into the honesty and high quality of the weld joint. Porosity, defined by the existence of cavities or voids within the weld steel, is a common problem in welding procedures. These gaps, otherwise correctly addressed, can compromise the structural integrity and mechanical properties of the weld, leading to prospective failures in the completed item.
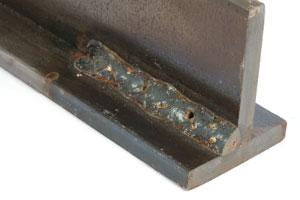
To discover and measure porosity, non-destructive screening techniques such as ultrasonic screening or X-ray evaluation are usually used. These strategies permit the identification of interior defects without endangering the integrity of the weld. By examining the dimension, shape, and circulation of porosity within a weld, welders can make informed decisions to boost their welding procedures and achieve sounder weld joints.
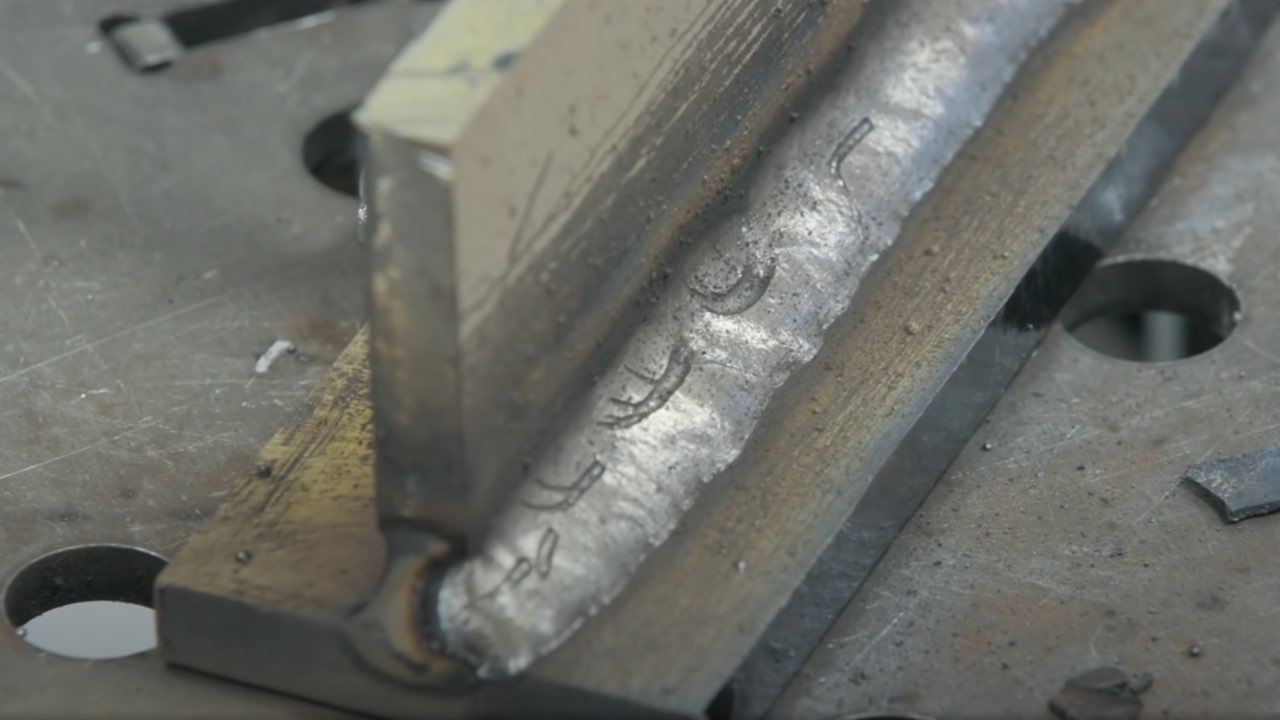
Elements Influencing Porosity Development
The incident of porosity in welding is affected by a myriad of aspects, varying from gas shielding efficiency to the complexities of welding specification setups. Welding specifications, consisting of voltage, current, take a trip rate, and electrode kind, additionally influence porosity development. The welding technique employed, such as gas steel arc welding (GMAW) or protected steel arc welding (SMAW), can affect porosity development due to variations in warm circulation and gas coverage - What is Porosity.
Effects of Porosity on Weld Quality
Porosity development significantly compromises the architectural integrity and mechanical residential or commercial properties of bonded joints. When porosity is existing in a weld, it produces voids or dental caries within the material, decreasing the overall stamina of the joint. These spaces serve as tension focus factors, making the weld a lot more prone to splitting and failing under load. The presence of porosity also damages the weld's resistance to deterioration, as the trapped air or gases within the spaces can react with the surrounding setting, leading to degradation over time. Furthermore, porosity can impede the weld's capacity to hold up against pressure or impact, more threatening the general top quality and dependability of the bonded structure. In critical applications such as aerospace, automobile, or architectural buildings, where safety and durability are extremely important, the detrimental impacts of porosity on weld high quality can have severe repercussions, stressing the value of decreasing porosity through proper welding techniques and treatments.
Methods to Reduce Porosity
To improve the high quality of welded joints and guarantee structural stability, welders and makers use specific methods targeted at minimizing the formation of spaces and cavities within the material throughout the welding process. One effective technique to reduce porosity is to make sure correct material preparation. This consists of comprehensive cleaning of the base metal to remove any type of impurities such as oil, oil, or wetness that might add to porosity development. Additionally, making use of the proper welding specifications, such as the proper Bonuses voltage, existing, and take a trip rate, is important in preventing porosity. Keeping a consistent arc length and angle throughout welding likewise helps lower the likelihood of porosity.

Making use of the suitable welding he said technique, such as back-stepping or using a weaving activity, can additionally help distribute warmth evenly and lower the possibilities of porosity development. By executing these strategies, welders can successfully lessen porosity and create top quality bonded joints.

Advanced Solutions for Porosity Control
Executing cutting-edge innovations and ingenious techniques plays a crucial duty in attaining exceptional control over porosity in welding processes. One advanced option is the use of sophisticated gas mixes. Shielding gases like helium or a mix of argon and hydrogen can help in reducing porosity by giving much better arc stability and boosted gas coverage. Furthermore, utilizing innovative welding strategies such as pulsed MIG welding or modified ambience welding can additionally aid minimize porosity problems.
An additional innovative option involves making use of innovative welding devices. Making use of equipment with integrated attributes like waveform control and sophisticated power resources can boost weld top quality and decrease porosity threats. Moreover, the implementation of automated welding systems with exact control over specifications can dramatically lessen porosity defects.
In addition, including sophisticated surveillance and evaluation innovations such as real-time X-ray imaging or automated ultrasonic testing can assist in discovering porosity early in the anonymous welding procedure, permitting instant rehabilitative actions. On the whole, integrating these sophisticated remedies can greatly boost porosity control and enhance the overall quality of bonded elements.
Conclusion
In conclusion, comprehending the science behind porosity in welding is necessary for welders and fabricators to produce high-quality welds - What is Porosity. Advanced options for porosity control can additionally improve the welding process and make certain a strong and trustworthy weld.
Report this page